Carbide punches are essential tools in various industries including manufacturing, metalworking, and construction. These punches are used to punch, punch or mark holes in a variety of materials including metal, plastic and wood. One of the key factors that affects the effectiveness and durability of carbide punches is the material they are made of.
Carbide punch are usually made of a material called tungsten carbide. Tungsten carbide is a compound formed by combining tungsten and carbon atoms through a sintering process. The process involves heating tungsten and carbon powder at high temperatures to form a solid, extremely hard material. Tungsten carbide is known for its exceptional hardness, wear resistance, and strength, making it an ideal choice for creating punches that can withstand the rigors of heavy-duty use.
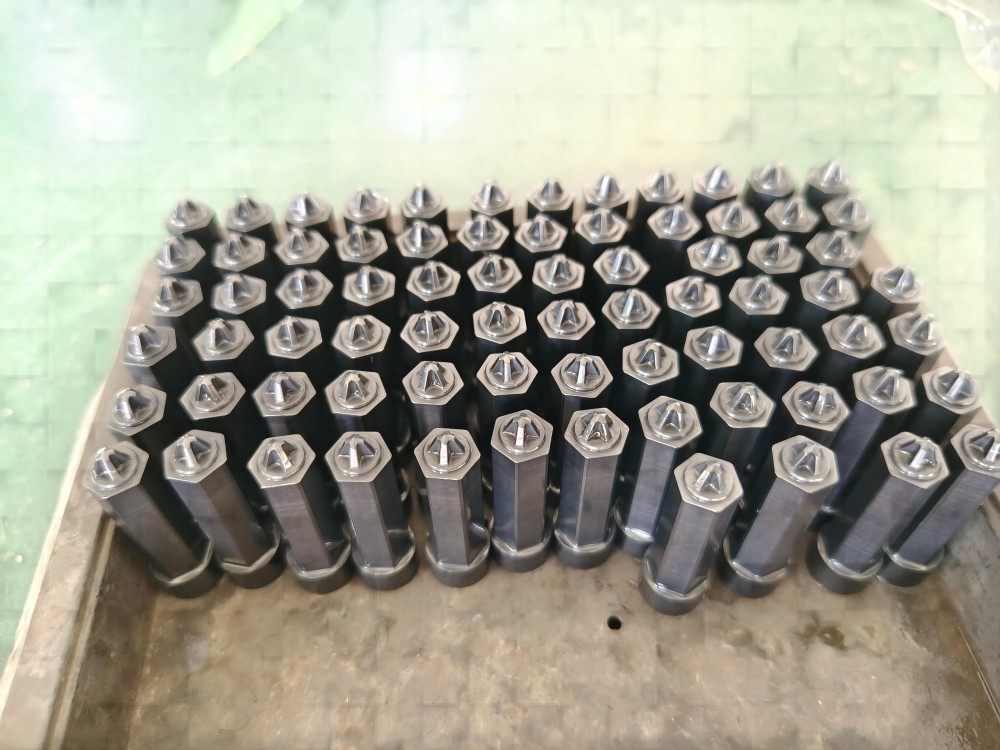
The hardness of tungsten carbide punches allows them to stay sharp and accurate over time, which makes them very effective when punching hard materials like steel, aluminum, and other metals. Additionally, the wear resistance of tungsten carbide ensures that the punch retains its shape and cutting edge, reducing the need for frequent sharpening or replacement.
In addition to tungsten carbide, carbide punches can be made from other materials to improve their performance and durability. For example, some carbide punches may contain a cobalt binder, which helps improve the punch's toughness and impact resistance. This is particularly beneficial in applications where the punch is subject to high impact or repeated use.
The manufacturing process of punch press dies involves precision machining and grinding to create the desired shape and cutting edge. This ensures that the punch meets tight dimensional tolerances and surface finish requirements, allowing it to deliver consistent and accurate results in a variety of punching applications.
Carbide punches are available in a variety of shapes and sizes to meet different stamping needs, including round, square, hexagonal and custom shapes. They are commonly used in industries such as metal fabrication, automotive manufacturing, aerospace and electronics, where precision stamping operations are critical to the production process.
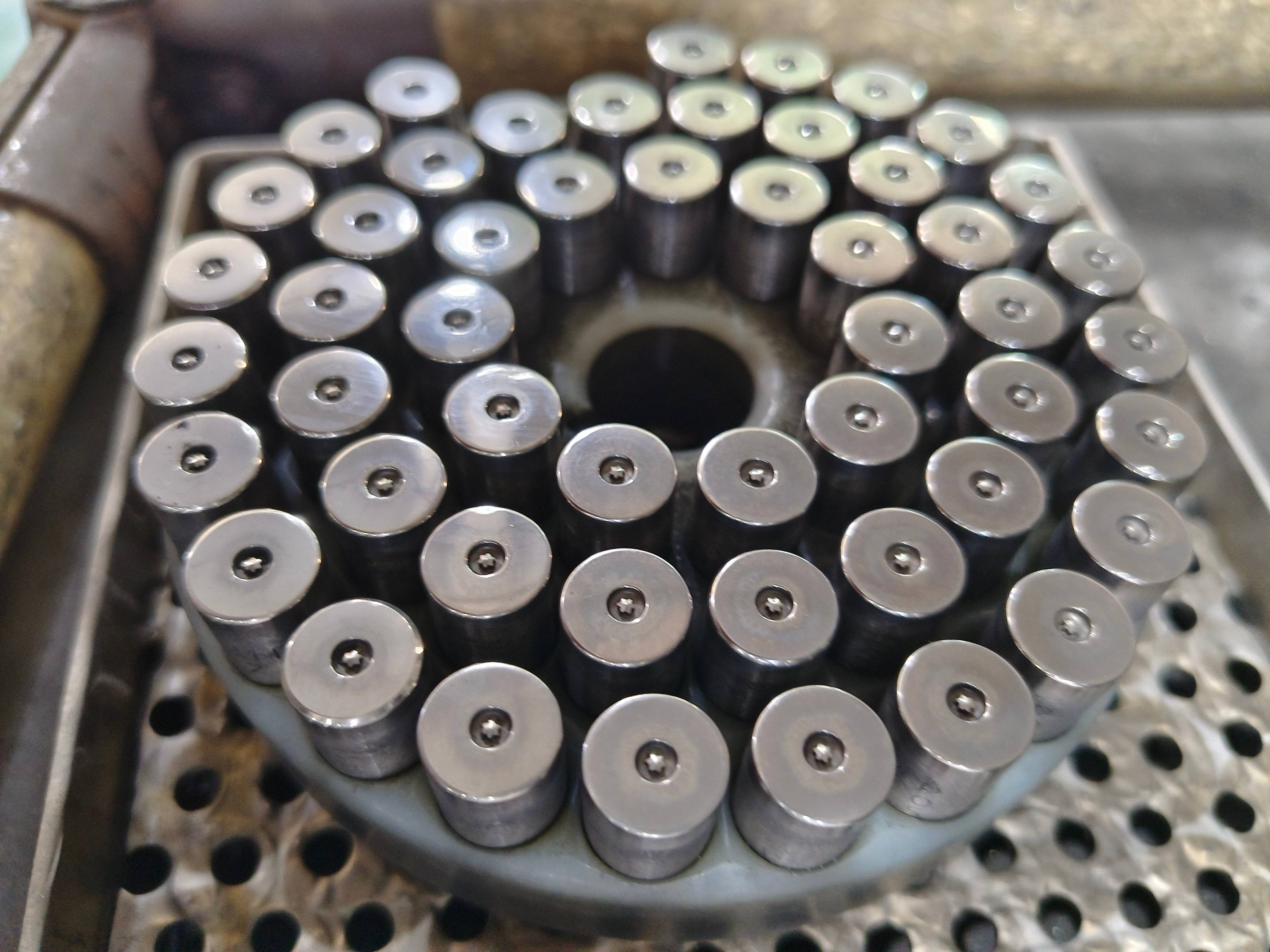
Post time: May-13-2024